
Custom Curtainwall Systems
Enclos offers the most innovative curtainwall systems in the marketplace, combining aesthetic, performance and economic considerations into optimum solutions to our client’s needs.Curtainwall anchors are set prior to the commencement of unit installation. If the anchors are to be recessed, they are sometimes set prior to the concrete floor slabs being poured, or provision is made for a cavity in the slab into which the anchor assembly will be installed.
Our inventive unitized systems have evolved through their application on numerous major building projects to represent the state-of-the-art in curtainwall technology and performance. Sophisticated system design features and installation methods have paralleled this evolution, resulting in improved economy as well as superior performance
Our inventive unitized systems have evolved through their application on numerous major building projects to represent the state-of-the-art in curtainwall technology and performance. Sophisticated system design features and installation methods have paralleled this evolution, resulting in improved economy as well as superior performance.
What Is Curtainwall

Curtainwall is a term applied to a widely used facade technology for cladding large buildings. Curtainwall systems do not carry any dead loads imposed from the building structure. They are designed to support their self-weight and to transfer horizontal loads (wind) incident upon them to the primary building structure.Curtainwall systems are typically “hung” from the building structure — from whence derives the “curtain” reference — and typically attached to the floor slabs. The primary functions of the curtainwall are to resist air and water infiltration and to provide a thermal barrier between inside and out. Curtainwall systems are also designed to accommodate the complexities of deflections, thermal expansion and contraction, building sway and relative movements between floors as caused by wind or seismic loads acting globally or locally on the structure.Special design considerations can include daylighting, thermal, acoustical, security and blast-resistant performance. Curtainwall designs for large buildings are almost always customized to individual project requirements.The craftsmanship required for AESS is a rare competency. We have developed a network of qualified AESS steel fabrication vendors, a network built over time and upon the experience of many successfully completed projects. Enclos is able to manage the delivery process in a manner that best assures predictability of outcome, thus mitigating the risk of budget overruns and schedule delays. Enclos’ QA programs fully incorporate AESS requirements.
Framing

Curtainwall is typically designed as cladding materials that are framed and fixed in place by extruded aluminum components. There are two basic types of systems :
-
Stick systems are built from long vertical extrusions (mullion) attached to the building structure, with shorter horizontal extrusions spanning between the vertical mullions to create the frames. Cladding materials are then installed into the frames. Extrusions may be fabricated in the shop, but all assembly, installation and glazing takes place in the field.
-
Unitized systems are a newer adaptation of curtainwall technology that has rapidly grown in use in recent years. The vertical and horizontal framing members are figuratively split, allowing independently framed “units” to be assembled and glazed in the factory. The units can be designed to span multiple floors or multiple horizontal modules, and can incorporate multiple cladding elements including operable vents and windows. The completed units are shipped to the site and simply hung on the building. Unitized systems concentrate fabrication and assembly under controlled factory rather than in the field. The selection between them is dependent upon project specific variables.
Enclos technical personnel can assist you in determining which system type is best for your particular project
Cladding

Glass is the most common infill material used in curtainwall systems, but other cladding materials include metal panels, natural stone and terracotta. The curtainwall systems typically span across the floor slabs, creating a need for opaque cladding material over and in the vicinity of the floor slab to conceal the slab edge, fire-safing and any between-floor mechanical systems. A spandrel panel is often located between vision glass panels to conceal this area. To achieve opacity, spandrel glass is treated with a ceramic coating (called a frit), a film, or is incorporated into an assembly called a shadow box.Glass is used extensively as a curtainwall cladding material because of its transparency and ability to provide daylight and view. Solar gain in such applications can present challenges with respect to energy performance, thermal and visual comfort, and represent important design considerations in the development of an appropriate curtainwall facade. Ongoing research and development has positioned the Enclos team to provide optimum solutions to these challenges, and has worked with leading architects in the development of high performance glass facades on many buildings pursuing LEED certification by the US Green Building Council.
Enclos has designed curtainwall systems for many LEED certified buildings
Facade Integration

In addressing the challenges discussed above, and in meeting the generally escalating performance demands on the building skin, curtainwall designs have become increasingly complex. Facade system requirements now frequently include daylight harvesting, daylight and glare control, artificial lighting, and even power generation. Techniques for addressing these considerations are being integrated into the curtainwall system, providing advanced functionality to the building facade. Photovoltaic systems, shade fins, light shelves, louvers, operable blinds, sensors and multiple skins are among the things being integrated into the curtainwall system.The building community has recognized the facade as a primary means to improve energy performance and occupant comfort, and even as a potential power source.
Anchorage
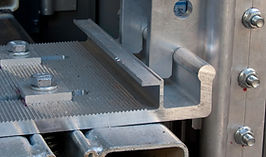
It is an exciting time for the development of advanced facade technology. At the same time, the fundamentals of sound curtainwall design have lost none of their critical import.One of the basic considerations that impacts every building project without exception is the means by which the curtainwall is anchored to the building. Anchor design can affect many things beyond the immediate curtainwall design, including the work of other trades and the design of the building interior. As with so many other aspects of the building skin, Enclos continues to lead the way with anchor design. Enclos anchor designs can be positioned on the face, top or bottom of slab, or recessed in any of these positions. The Enclos anchoring method is highly efficient, speeds field installation of the curtainwall and provides optimum economy to the building developer.
Installation

Installation strategy is highly sensitive to specific site, schedule and coordination requirements. All Enclos operations are driven by the requirements of the building site.Unitized curtainwall systems provide optimum flexibility in this regard. Materials can be fabricated, assembled and stored offsite, and be delivered on a just-in-time basis as required to support installation crews, thus minimizing on-site storage and staging requirements on highly congested building sites. Assembled units are delivered to the site on open flatbed trailers. The units can be lifted by crane from the trailer and directly set in place on the building facade. Alternately, units can be designed to be installed from inside the building. Installation crews working from a floor above use a small jib crane to lower the units to a setting crew below. Other techniques are possible depending upon specific project requirements.Installation strategy, site logistics and operations are among the greatest strengths of Enclos, and represent the capability most valued by our general contracting clients.
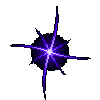