
Architecturally Exposed Structural Steel (AESS)
The art of steel. Structural glass facades are not simply about transparency. Often the designer seeks to express the structural system supporting the facade, sometimes even at the expense of transparency. What is necessarily required here is a level of craftsmanship that extends far beyond what is found in conventional structural steel.
The AISC specification for Architecturally Exposed Structural Steel (AESS) is often applied to structural glass facade designs. These designs frequently include exposed structural systems in high profile public areas, such as building lobbies and atria, and as long-span facade systems in airports, museums, and government buildings.
The AESS spec is intended to provide the designer a means to control the visual quality of structural steel used in such applications. However, this specification is no panacea to the problem of communicating the requirements for visual quality such that the same expectations are shared by all relevant parties. An AESS Supplement published by Modern Steel Construction states, “Unfortunately, existing codes and standards — even AISC’s Code of Standard Practice — do not fully address the unique level of detail needed to successfully design, detail, fabricate and erect Architecturally Exposed Structural Steel (AESS).”
Enclos has designed and provided many AESS structures as part of its custom facade work. We understand the demanding design, fabrication, assembly and installation requirements involved in the successful implementation of this specification, and we can bring this valuable capability to your team.
Exposed Structural Systems
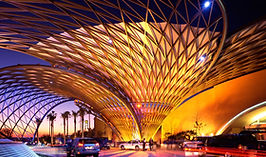
The use of transparency and exposed structural systems in architectural design go hand-in-hand. While structural glass facade systems make frequent use of cables, rods, and machined fittings, they also often include fabricated steel assemblies ranging from exposed anchor components to custom truss systems. The craftsmanship required for AESS is a rare competency. We have developed a network of qualified AESS steel fabrication vendors, a network built over time and upon the experience of many successfully completed projects. Enclos is able to manage the delivery process in a manner that best assures predictability of outcome, thus mitigating the risk of budget overruns and schedule delays. Enclos’ QA programs fully incorporate AESS requirements
Weld Quality and Workmanship

An important consideration with exposed structural steel is the treatment of welds. Designers often want welds to be ground flush and smooth, sometimes even polished. However, primary consideration must be given to the structural integrity of the weld. Accommodating both the structural performance requirements and the desired appearance starts as a critical design issue; welds must be designed such that both criteria can be satisfied in the fabrication and finishing processes. We are practiced at controlling this process from concept design through completed fabrication. The fit-up requirements for bolted connections can be an equally important consideration.
Budgeting

The AESS Supplement comments, “…because AESS costs more to fabricate than standard structural steel, it is critical that these designs are properly budgeted. The repercussion of not properly budgeting AESS is often the need for redesign, project delays, and ultimately even higher project costs.”
The budget for AESS is affected by subtle decisions regarding material, surface quality, weld quality and finish. Whether the concern is for welds, finishes, budgeting or any other aspect of AESS, Enclos can act as an expert guide through the maze of decision making to best assure the development of an appropriate AESS specification and its effective implementation.
Finishes
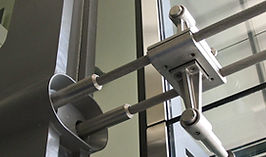
Red iron rusts. Of the many great attributes of steel, this is not one of them. Exposed structural steel must be protected, and most often the finish requirements are meant to augment the appearance of the structure and not merely to protect the steel.
The term “automotive finish” is frequently heard yet seldom achieved. Hot-dipped galvanizing can provide superior protection with a top color coat for appearance.
Most steel fabrications are too large for this process however, and there are environmental concerns regarding its use. The application of paint over a galvanized surface can be tricky as well.
Various other paint systems exist, most involving the application of a primer coat over a carefully prepared surface, followed by one or two color top coats. Metallic finishes are available and have been used successfully in a number of applications. A key decision is whether to apply the final coat in the field or in the shop.
Shop application is invariably superior, but almost certainly subject to damage during shipping, assembly and erection even when extensive precautions are taken to protect the finish. A field touchup specification is as important as the basic finish specification in the case of factory applied finish.
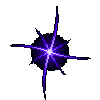